Upgrading Your Eye Wash Station: When and Why to Replace Parts
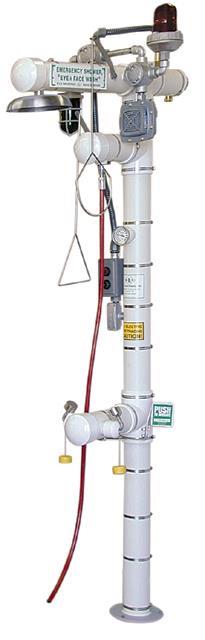
Ensuring the optimal performance of your eye wash station is crucial for maintaining workplace safety, especially in environments where hazardous materials are present. Regular maintenance and timely replacement of parts not only comply with safety regulations but also protect the well-being of your employees.
Signs Your Eye Wash Station Needs an Upgrade
An eye wash station is a critical piece of safety equipment designed to mitigate eye injuries caused by exposure to chemicals, debris, or hazardous substances. However, over time, the station’s components can degrade due to factors like corrosion, mineral deposits, or general wear. Identifying the signs of wear and tear early can prevent potential failures and ensure compliance with safety standards.
Age and Wear Indicators
Over time, the materials and components in your eye wash station can deteriorate, compromising its effectiveness. Signs that parts may need replacement include:
- Corroded or Rusty Parts: Metal components showing signs of rust or corrosion can weaken and eventually fail, reducing the reliability of the station.
- Cracked or Brittle Materials: Plastic or rubber parts may become brittle, crack, or lose flexibility, leading to leaks and ineffective performance.
- Reduced Water Flow: Clogged nozzles or malfunctioning flow regulators can result in insufficient water flow, preventing proper eye irrigation.
- Leaking Seals or Connections: Water leaks indicate that seals, gaskets, or fittings may be deteriorating and require replacement.
- Outdated Components: Older models may not meet current ANSI Z358.1 safety standards, requiring upgrades to ensure compliance.
According to OSHA guidelines, eyewash stations should be inspected weekly to ensure proper operation and functionality. A thorough annual inspection should also be performed to assess the condition of components and replace any that are worn or outdated.
Essential Parts of an Eye Wash Station
Understanding the key components of your eye wash station is crucial for effective maintenance and timely replacements. Here are the main parts that should be regularly inspected and replaced when necessary:
- Nozzles: These direct the flow of water to the eyes and should be free from blockages and mineral buildup.
- Activation Valve: A properly functioning valve ensures that water flows immediately upon activation.
- Bowl or Receptacle: Collects wastewater during use and should be free from cracks or damage.
- Dust Covers: Protect nozzles from contaminants and should be replaced if missing or damaged.
- Flow Regulator: Ensures that water is delivered at a safe and adequate pressure for effective eye irrigation.
- Signage and Lighting: Proper labeling and illumination ensure that the station is easily identifiable during emergencies.
Regular cleaning and testing of these components help maintain the eye wash station’s functionality and prevent failures during critical situations.
Choosing Quality Replacement Parts
Selecting the right replacement parts ensures the longevity and reliability of your eye wash station. When choosing replacement components, consider the following factors:
Compatibility with Existing Systems
Not all replacement parts are universally compatible with every eye wash station model. When purchasing parts, ensure they match the specifications of your existing system. It is advisable to use parts from the original manufacturer or those that meet ANSI standards to maintain compliance and reliability.
Manufacturers such as B-L-S Industries, Inc. provide high-quality replacement parts specifically designed for various emergency wash stations. Choosing parts from reputable suppliers ensures durability and performance.
Cost vs. Benefit of Upgrades
While cost is a consideration, investing in high-quality parts can prevent future failures and potential safety hazards. Balancing initial expenses with long-term benefits is crucial. A well-maintained eye wash station reduces the risk of workplace injuries, minimizing liability and potential OSHA violations.
Upgrading older stations to meet the latest safety standards can also be a cost-effective investment in workplace safety. Features such as self-draining nozzles, enhanced flow control, and heated units for cold environments can provide added safety and convenience.
When to Upgrade Instead of Repairing
In some cases, replacing individual components may not be enough to ensure full compliance and reliability. If your eye wash station exhibits frequent malfunctions, is outdated, or does not meet ANSI Z358.1 standards, it may be time to upgrade to a newer model.
Benefits of Upgrading
- Improved Safety Compliance: Newer models are designed to meet current regulations, ensuring workplace safety and legal compliance.
- Enhanced Performance: Modern stations provide improved water flow, better accessibility, and additional safety features.
- Reduced Maintenance Costs: Upgrading to a more reliable system can reduce the need for frequent repairs and part replacements.
- Adaptation to Workplace Needs: Advanced features such as heated water systems, hands-free activation, and increased capacity can enhance safety in demanding environments.
If your current station is over a decade old or shows significant wear despite regular maintenance, consider investing in a new unit that offers better safety and efficiency.
Ensuring Compliance with Safety Standards
The American National Standards Institute (ANSI) and the Occupational Safety and Health Administration (OSHA) have strict regulations regarding eye wash stations. ANSI Z358.1 sets the standards for installation, performance, and maintenance, requiring:
- Weekly activation of the station to flush out stagnant water.
- Annual inspections to ensure compliance and functionality.
- Unobstructed access to the station within 10 seconds of hazardous areas.
- Continuous water flow of at least 15 minutes at the correct pressure and temperature.
Failing to meet these standards can result in non-compliance penalties and increased liability risks. Routine inspections and timely part replacements ensure that your station remains in compliance with these regulations.
Partnering with B-L-S Industries, Inc. for Your Eye Wash Station Needs
Regular maintenance and timely upgrades of your eye wash station are essential for workplace safety. By staying vigilant and proactive, you can ensure that your equipment remains reliable, compliant, and effective in an emergency situation.
At B-L-S Industries, Inc., we are committed to providing top-quality emergency drench showers and eye and face wash stations. Based in Carl Junction, MO, we have been a trusted supplier of workplace safety equipment since 1976. With over four decades of experience, we understand the importance of durable and compliant safety solutions.
Whether you need replacement parts, a new eye wash station, or custom-designed safety solutions, we have the expertise to meet your needs. Our mission is to ensure your employees are protected in the event of an emergency with reliable, high-performance safety equipment.
Don’t wait until an emergency exposes a weakness in your safety system. Contact us today to learn more about our products and how we can help keep your workplace safe.