The Hidden Risks: Ensuring Your Eye Wash Station is Ready for an Emergency
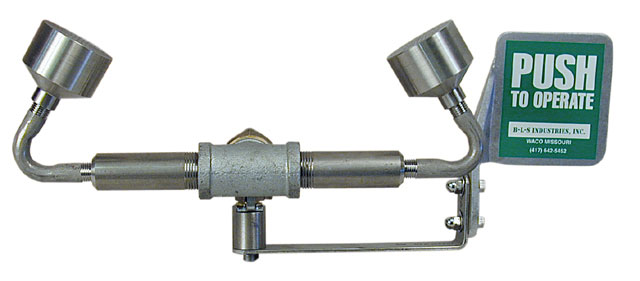
When an emergency occurs in the workplace, every second counts. Employees exposed to hazardous chemicals or debris need immediate access to functional safety equipment like eye wash stations to mitigate injury risks. However, the effectiveness of these stations depends heavily on their readiness—a factor determined through consistent maintenance and eye wash station inspection. Neglecting this vital process can lead to severe consequences, not only for employee health but also for regulatory compliance and business operations.
Let’s explore why regular eye wash station inspections are essential, the critical components to check, and how maintaining compliance can ensure workplace safety.
Why Regular Eye Wash Station Inspections Are Crucial for Workplace Safety
An eye wash station is a lifeline for employees working in environments with chemical, biological, or particulate hazards. Ensuring these systems are fully operational can mean the difference between a minor irritation and long-term vision damage—or worse. Yet, many businesses underestimate the importance of regular inspections, exposing themselves to a host of hidden risks.
Protecting Employee Health and Safety
Eye wash stations are designed to deliver immediate relief during emergencies, preventing hazardous substances from causing permanent damage. However, without regular inspections, these stations may not function as intended. Blocked nozzles, low water pressure, or contaminated water can render an eye wash station useless, delaying critical first aid and exacerbating injuries.
Avoiding Regulatory Penalties
Workplace safety regulations, such as those established by the Occupational Safety and Health Administration (OSHA), mandate that eye wash stations meet strict standards. Failure to perform routine inspections can lead to non-compliance, resulting in hefty fines, legal liabilities, and damaged reputations.
Minimizing Operational Downtime
An inoperative eye wash station can lead to workplace accidents that disrupt productivity. Inspections help identify potential issues before they become critical, ensuring smooth operations and minimizing costly interruptions.
Key Areas to Inspect to Ensure Your Eye Wash Station is Emergency-Ready
Effective eye wash station inspection involves evaluating multiple components to guarantee functionality and compliance. Each inspection should be thorough, addressing both visible and underlying issues.
Visual and Functional Checks for Eye Wash Stations
- Nozzle Cleanliness: Ensure that nozzles are free from debris, mineral deposits, or contamination that could compromise water flow or introduce additional hazards during use.
- Water Flow and Pressure: Verify that the station delivers tepid water (60-100°F) at the correct flow rate, as specified by ANSI/ISEA Z358.1 standards.
- Activation Mechanism: Test the activation handles or levers for ease of use. They must be operable within one second or less and stay activated without manual assistance.
- Drainage and Overflow: Check that excess water drains properly, preventing flooding or slip hazards around the station.
- Signage and Accessibility: Confirm that the station is clearly marked and free from obstructions, ensuring employees can locate and access it quickly in an emergency.
Common Issues Found During Eye Wash Station Inspections
Even the most well-designed eye wash stations can develop issues over time. Some of the most common problems uncovered during inspections include:
- Corroded or Leaking Pipes: Rust and leaks can affect water quality and pressure, reducing the station’s effectiveness.
- Contaminated Water Supply: Stagnant water in infrequently used stations can harbor bacteria, posing additional risks to users.
- Obstructed Access: Storage items, furniture, or equipment blocking access to the eye wash station can delay critical response times.
- Inadequate Water Temperature: Water that is too hot or too cold can cause discomfort, discouraging employees from using the station for the recommended 15 minutes.
How Often Should You Inspect Your Eye Wash Station for Compliance?
Eye wash stations should undergo regular inspections to maintain compliance with OSHA and ANSI standards. These evaluations not only ensure the system’s readiness but also provide peace of mind for both employers and employees.
Weekly Flush Tests
Perform a quick activation of the station each week to confirm proper water flow and remove stagnant water from the pipes. This simple step prevents sediment build-up and ensures the station remains functional between full inspections.
Annual Inspections
Conduct a comprehensive eye wash station inspection at least once a year. This process should include detailed testing of water pressure, temperature, and flow rate, along with an assessment of all components for wear and tear.
After Hazardous Events
Whenever a workplace incident occurs—such as a chemical spill or equipment malfunction—inspect the eye wash station to verify it remains fully operational. Post-incident inspections help identify and address damage caused during emergencies.
Documenting and Reporting Eye Wash Station Inspections for Compliance
Accurate documentation of inspections is critical for demonstrating compliance and identifying patterns that could indicate recurring issues. Maintaining thorough records can also streamline communication with safety regulators and internal stakeholders.
Keeping Inspection Logs
Record the date, time, and findings of each inspection, along with the name of the person conducting it. Logs should include details of any maintenance performed or parts replaced.
Reporting Issues
Any deficiencies discovered during inspections should be reported and addressed promptly. Outline the steps taken to resolve the problem and include this information in your records to show due diligence.
Auditing Records
Periodically review your inspection logs to ensure completeness and accuracy. Audits can reveal trends or recurring issues, helping you implement preventive measures and improve safety protocols.
Protect Your Workforce with B-L-S Industries, Inc.
An effective eye wash station can save lives—but only if it’s ready when you need it most. Routine inspections are a vital step in maintaining compliance and ensuring the safety of your employees in hazardous environments. At B-L-S Industries, Inc., we’ve been committed to providing top-quality emergency drench showers and eye and face wash stations since 1976.
Based in Carl Junction, MO, we offer a comprehensive range of safety solutions, including standard eye wash stations, custom-designed units, and heated shower enclosures. With over four decades of experience, we understand the critical importance of workplace safety and take pride in delivering reliable, compliant, and durable products that protect your employees and your business.
Contact us today to explore our wide range of safety equipment and discover how we can help you maintain a safe and compliant workplace. Let’s ensure your safety equipment is always ready for an emergency—because your team deserves nothing less.