Industrial Drench Showers: When and Where You Need Them
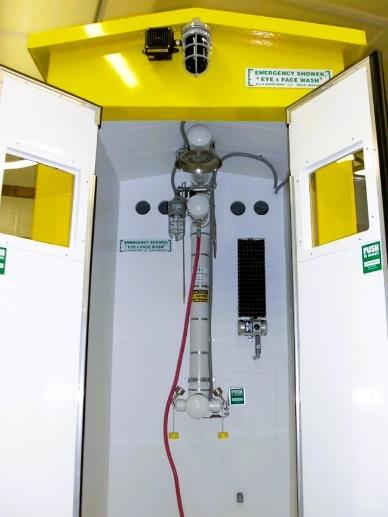
Even the most robust safety protocols can’t always prevent accidents in hazardous work environments. When exposure to corrosive chemicals, extreme heat, or toxic substances occurs, time is of the essence—and that’s where drench showers come into play.
Industrial drench showers are not just a regulatory checkbox—they’re a critical component of your emergency response system. Designed to quickly and thoroughly flush contaminants from the body, these safety stations can mean the difference between a minor incident and a life-altering injury. Whether you’re operating in a chemical processing plant or a food production facility, understanding when and where you need a drench shower—and how to maintain it—can significantly impact your employees’ safety and your regulatory compliance.
What Are Drench Showers?
Drench showers are emergency devices designed to provide a high flow of water for flushing the body in the event of exposure to hazardous substances. Unlike eye or face wash stations that target specific areas, drench showers are full-body systems that deliver a deluge of water to rapidly remove harmful materials.
These showers are often found in environments where workers are at risk of:
- Chemical splashes or spills
- Exposure to flammable or toxic materials
- Thermal burns
- Biological contaminants
A standard drench shower delivers 20 gallons per minute (GPM) of water for a minimum of 15 minutes. Their effectiveness depends on immediate access, proper installation, water pressure and temperature, and ongoing maintenance.
Industries That Require Drench Showers
Numerous sectors rely on drench showers to meet both operational safety needs and OSHA/ANSI compliance requirements. Here are a few industries where drench showers are not just recommended—they’re essential:
- Chemical manufacturing and processing – For handling corrosive acids, alkalis, and solvents.
- Pharmaceuticals – Where raw materials and reagents pose a risk to skin or eyes.
- Oil and gas – Particularly in drilling, refining, or transportation settings.
- Mining – For exposure to toxic dust or chemicals used in ore processing.
- Food and beverage – To handle cleaning agents, hot liquids, and chemical additives safely.
- Laboratories and research facilities – Where hazardous experiments and substances are routine.
- Water treatment plants – Where workers handle chlorine, ammonia, and other potent chemicals.
Any workplace involving exposure to dangerous chemicals or substances should consider emergency drench showers a non-negotiable safety feature.
When Are Drench Showers Required?
Organizations must understand when drench showers are legally or operationally required to ensure compliance and minimize liability. The primary standards that govern this area are from OSHA (Occupational Safety and Health Administration) and ANSI (American National Standards Institute).
OSHA Regulations
OSHA mandates that employers provide “suitable facilities for quick drenching or flushing of the eyes and body” in areas where employees may be exposed to injurious corrosive materials (OSHA 29 CFR 1910.151(c)). While OSHA doesn’t specify technical details, it defers to ANSI Z358.1 for guidance.
ANSI Z358.1 Standard
The ANSI Z358.1 standard outlines precise requirements for emergency showers, including:
- Activation time: Must be accessible in under 10 seconds from the hazard.
- Flow rate: Minimum 20 GPM for at least 15 minutes.
- Water temperature: Tepid (60–100°F or 16–38°C).
- Location: Must be on the same level and unobstructed.
- Hands-free operation: Once activated, the unit must operate without the user holding it open.
Risk Assessments
Beyond regulations, companies should conduct hazard assessments to determine where and how many drench showers are needed. Consider factors such as:
- The volume and type of hazardous materials handled
- Worker proximity to potential spills
- Size and layout of the facility
- Time required to reach the nearest shower
In high-risk facilities, multiple strategically placed drench showers may be necessary to ensure coverage in all exposure zones.
How to Maintain and Test Drench Showers
An emergency drench shower is only effective if it works flawlessly when needed. Regular testing and maintenance are vital not only for compliance but also for ensuring the safety of every person on-site.
Weekly Activation Tests
According to ANSI Z358.1, drench showers should be activated weekly to:
- Confirm water flow
- Clear sediment buildup in plumbing
- Ensure valves and nozzles aren’t clogged
- Prevent stagnation and bacterial growth (such as Legionella)
Annual Full Inspections
A more detailed inspection should be carried out annually to verify compliance with all ANSI requirements. This includes:
- Confirming flow rate and spray pattern
- Testing temperature range
- Checking for physical obstructions
- Verifying signage and lighting visibility
- Inspecting drain systems and enclosure integrity (if applicable)
Water Pressure & Temperature Considerations
To function correctly, drench showers require sufficient water pressure, flow rate, and temperature control.
- Pressure: The minimum water pressure should support 20 GPM at 30 PSI.
- Temperature: Tepid water (between 60°F and 100°F) is critical to prevent hypothermia or scalding.
- Heated enclosures: In outdoor or unconditioned spaces, consider heated or insulated drench shower systems to prevent freezing in winter and ensure consistent tepid water.
Fluctuations in water pressure or temperature can render even the best system ineffective. Regular checks ensure that the system is always ready to go.
Common Maintenance Mistakes
Even well-meaning facility managers can fall short in maintaining drench showers. Here are a few common pitfalls to avoid:
- Obstructed access – If a forklift or storage bin blocks the unit, it’s practically useless in an emergency.
- No drainage – Standing water can create slip hazards and hygiene issues.
- Poor documentation – Without proper test records, proving compliance during an audit becomes difficult.
- Ignoring outdoor conditions – In cold climates, failing to install freeze-protected or heated models is a major liability.
- Using cold or scalding hot water – Tepid water is not optional—it’s essential for safety and compliance.
Avoid these errors by working with an experienced supplier who understands the nuances of emergency equipment design, installation, and upkeep.
Best Practices for Emergency Response
A properly installed and maintained drench shower is just one piece of the emergency preparedness puzzle. Here are some best practices to integrate drench showers into your broader safety protocols:
- Train employees regularly – Everyone should know where the nearest shower is, how to use it, and when to use it.
- Clearly mark all units – Use highly visible signage with glow-in-the-dark or photoluminescent features in low-light areas.
- Run drills – Incorporate shower activation into chemical spill or exposure drills to build muscle memory and reduce panic.
- Evaluate response times – Ensure showers are accessible within 10 seconds of any hazard point. That may mean reevaluating the layout or adding more units.
- Install alarms – Some units can be connected to alert systems, which notify management when a shower is activated, speeding up medical response.
Remember, seconds count. The first few moments after exposure are critical for minimizing injury and improving recovery outcomes.
Why B-L-S Industries, Inc. Is Your Trusted Partner in Workplace Safety
At B-L-S Industries, Inc., we’ve been committed to providing top-quality emergency drench showers and eye and face wash stations since 1976. Based right here in Carl Junction, MO, we understand the real-world challenges businesses face when trying to implement safe, compliant, and reliable emergency systems.
Our team offers more than just products—we offer tailored solutions backed by decades of engineering expertise. From standard wall-mounted units to custom-designed heated enclosures, every piece of equipment we produce is crafted to exceed ANSI and OSHA standards.
Whether you need a single unit or an entire facility outfitted with state-of-the-art drench showers and eyewash systems, B-L-S Industries has the experience, durability, and technical know-how to deliver.
Ready to Upgrade Your Emergency Response Systems?
You can’t afford to take chances when it comes to workplace safety. Let B-L-S Industries, Inc. be your go-to resource for drench showers and emergency wash solutions. Our commitment to reliability, compliance, and long-lasting performance ensures your workforce stays protected—no matter the hazard.
Explore our full line of drench showers, eyewash stations, and custom safety systems, and reach out today to talk to one of our safety equipment specialists. With over four decades of innovation and customer service, we’re proud to help you protect what matters most—your people.