Everything You Need to Know About Safety Showers
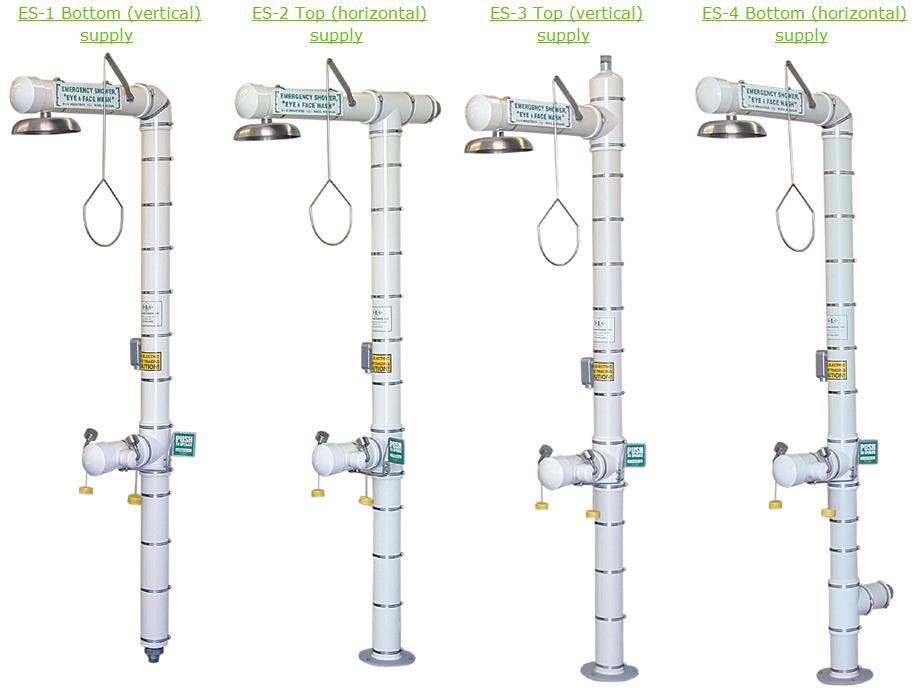
In hazardous work environments, time is of the essence when an emergency strikes. Whether it’s a chemical splash, exposure to a corrosive substance, or thermal burns, a quick and effective response can mean the difference between a full recovery and permanent damage. This is where the safety shower becomes an essential part of any facility’s emergency preparedness plan.
At B-L-S Industries, Inc., we’ve spent nearly 50 years designing and supplying industrial-grade emergency drench showers and eye wash stations for companies across the U.S. From our headquarters in Carl Junction, MO, we understand the unique safety needs of businesses working with hazardous materials.
What is a Safety Shower?
A safety shower is an emergency fixture designed to flush the body with copious amounts of water in the event of exposure to harmful chemicals, substances, or high heat. These showers are typically found in industrial facilities, laboratories, manufacturing plants, and other high-risk environments. They are not designed for personal hygiene but rather to deliver immediate decontamination to limit injury.
Most safety showers are activated by a pull handle or push plate and must release a high flow of water instantly to be effective. In many cases, safety showers are paired with eye and face wash stations to ensure that sensitive areas such as the eyes are protected as well.
When Are Safety Showers Required?
OSHA regulations and ANSI standards dictate that safety showers are necessary in any workplace where employees are at risk of being exposed to:
- Corrosive chemicals
- Flammable or toxic substances
- Particulates that can cause skin irritation
- Thermal injuries or extreme heat
These units must be readily accessible within 10 seconds of potential exposure and must be able to operate hands-free for a full 15-minute rinse.
Key Safety Standards for Safety Showers
Ensuring compliance with key regulations is critical to both safety and liability. The most widely recognized standard for safety showers and eyewash stations is ANSI/ISEA Z358.1.
ANSI Standards Explained
The ANSI/ISEA Z358.1 standard outlines the minimum performance and installation requirements for safety showers. Let’s take a closer look at some of the key specifications:
- Location & Accessibility: The safety shower must be within 10 seconds of the hazard area and have an unobstructed path for access.
- Flow Rate: The shower must deliver a minimum of 20 gallons per minute (GPM) for at least 15 minutes.
- Water Temperature: To prevent thermal shock or hypothermia, tepid water, defined as between 60°F and 100°F, is required.
- Activation: Must be easily activated within one second and remain on without the user holding the handle.
- Testing Requirements: Weekly functional testing and annual performance testing are required to ensure continued compliance.
Facilities that fail to comply with ANSI/ISEA Z358.1 may face fines, injuries, and potential legal action. More importantly, non-compliance can seriously risk employee health.
Choosing the Right Safety Shower
With so many options available, selecting the appropriate safety shower for your facility involves more than just meeting the minimum standard. Factors like environmental conditions, the nature of hazards, and user comfort should be taken into account.
Let’s examine the different types of safety showers and the criteria for selecting the right one.
1. Indoor vs. Outdoor Showers
- Indoor Showers: Common in laboratories and indoor manufacturing plants. These are easier to install and often benefit from existing climate control.
- Outdoor Showers: Require weather protection. Heated enclosures or freeze-protected units are critical in colder climates to maintain tepid water and prevent freezing.
2. Plumbed vs. Self-Contained Showers
- Plumbed Units: Connected directly to the facility’s water supply. Reliable and continuous water flow but requires proximity to plumbing infrastructure.
- Self-Contained Units: Use a tank to store water. Ideal for remote or temporary job sites. These need to be regularly refilled and inspected.
3. Combination Units
Many workplaces opt for combination units that include both a full-body shower and an eye/face wash station. These provide comprehensive coverage in one installation, especially valuable in areas with multiple potential hazards.
4. Specialty Showers
Some environments require more specific equipment:
- Corrosive Material Showers: Resistant materials like stainless steel or coated parts are crucial.
- Heated Enclosures: Maintain tepid water even in freezing conditions.
- Portable Units: For temporary job sites, mobile labs, or field work.
5. Flow Control and Drainage
Don’t overlook drainage and water management. A high-capacity emergency shower can release over 300 gallons in 15 minutes. Proper drainage systems are necessary to prevent flooding and slip hazards.
How to Maintain a Safety Shower
Even the best-designed safety shower won’t protect workers if it’s not properly maintained. Routine maintenance ensures readiness and compliance with safety regulations.
Weekly Checks Should Include:
- Flushing the unit to remove sediment buildup
- Ensuring water flow activates within 1 second
- Checking for obstructions and proper signage
Annual Inspections Should Include:
- Verifying flow rates and spray patterns
- Temperature testing for tepid water compliance
- Inspection of valves, pipes, and structural integrity
A maintenance log should be kept to document inspections, identify trends, and provide evidence of compliance if needed.
Common Issues and Troubleshooting
Here are some common issues that can affect the performance of a safety shower—and what to do about them:
Problem: Inadequate Water Flow
- Cause: Blocked or corroded pipes or poor water pressure
- Solution: Flush lines weekly; check for buildup and repair or replace faulty components.
Problem: Water Too Cold or Too Hot
- Cause: Lack of tempering valve or malfunctioning heater
- Solution: Install a thermostatic mixing valve; insulate or heat pipes in cold climates.
Problem: Inaccessible Shower
- Cause: Poor placement or obstructed path
- Solution: Re-evaluate shower location; ensure it’s clearly marked, unobstructed, and within 10 seconds of hazard zones.
Problem: Eye Wash Nozzles Clogged
- Cause: Debris or mineral buildup
- Solution: Use protective covers on nozzles; include nozzle cleaning in weekly tests.
Regular training for employees is also key. Staff should know:
- Where each safety shower is located
- How to operate it correctly
- When to use it
Partnering with a Trusted Safety Shower Provider
When it comes to workplace safety, your equipment is only as reliable as the company behind it. That’s why industries across the country trust B-L-S Industries, Inc. for their emergency shower and eye wash solutions.
Since 1976, we’ve been designing, engineering, and manufacturing top-quality safety showers, eye wash stations, and drench equipment right here in Carl Junction, Missouri. Our team understands the technical and regulatory demands that come with hazardous environments—from chemical plants and industrial labs to mining and food processing.
Whether you need a:
- Standard ANSI-compliant safety shower
- Customized solution for unique applications
- Freeze-protected or heated enclosure
- Combination shower/eye wash unit
—we’ve got you covered.
Our products are built for durability, simplicity, and maximum compliance. But beyond that, we offer something that’s harder to find: a knowledgeable team that truly cares about your safety. We consult with clients to understand their work environments, regulatory requirements, and infrastructure challenges so we can recommend the right system the first time.
Ready to Upgrade Your Workplace Safety?
If your facility handles chemicals, corrosives, or thermal processes, having the right safety shower solution in place isn’t just a regulatory box to check—it’s a critical part of your emergency response plan. Choosing the right equipment, installing it correctly, and keeping it in top shape can protect your employees and your business from devastating injuries and costly penalties.
B-L-S Industries, Inc. is here to help every step of the way. From standard eye wash stations to custom-engineered drench solutions and fully enclosed heated systems, we provide safety products that are built to last, made to comply, and designed to perform when seconds count. Contact us today.