Top Tips for Maintaining Eye Wash Stations and Drench Showers in Industrial Facilities
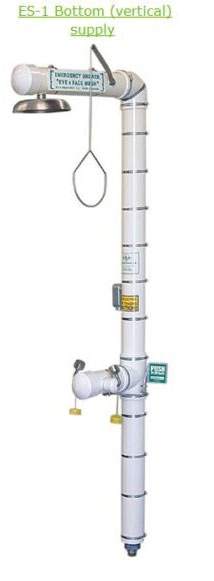
Industrial facilities present unique hazards where safety showers and eye wash stations are vital. These emergency fixtures are the first line of defense against chemical splashes, burns, or debris in the eyes. Proper maintenance ensures these systems function effectively during emergencies and comply with industry safety standards. Neglecting routine upkeep can compromise their effectiveness, jeopardizing employee safety and resulting in regulatory penalties.
Why Regular Maintenance of Safety Showers and Eye Wash Stations is Essential
The Role of Safety Showers and Eye Wash Stations
Safety showers and eye wash stations are critical for mitigating injuries in environments where hazardous materials are handled. These systems provide immediate decontamination to reduce the severity of exposure to harmful substances. They are especially important in chemical manufacturing, laboratories, and industrial plants where employees are at risk of encountering corrosive chemicals or flying particles.
Compliance with Industry Standards
Organizations like the Occupational Safety and Health Administration (OSHA) and the American National Standards Institute (ANSI) establish strict requirements for safety shower performance. ANSI Z358.1-2014, for example, outlines specific guidelines for flow rate, water temperature, and accessibility. Regular maintenance ensures compliance, avoiding costly fines and maintaining a safe work environment.
Protecting Employee Health and Reducing Liability
Well-maintained safety showers reduce the risk of injury by providing reliable emergency response tools. Neglected equipment can malfunction, exacerbating injuries and increasing the employer’s liability. Proactive maintenance demonstrates a commitment to employee safety and fosters trust among the workforce.
Key Maintenance Steps for Industrial Safety Showers
Maintaining safety showers and eye wash stations involves a series of routine tasks that ensure the equipment is operational, clean, and compliant.
Cleaning and Testing Procedures for Optimal Performance
Flush Systems Weekly:
ANSI recommends activating safety showers and eye wash stations weekly to flush out stagnant water and contaminants. This also verifies that the system delivers an adequate flow rate.
Inspect Nozzles and Heads:
Check for blockages, cracks, or mineral deposits that can impair water flow. Clean components with appropriate tools and solutions to remove buildup.
Monitor Water Temperature:
Water should be tepid (60–100°F) to prevent thermal shock or further injury. Install a thermometer to regularly monitor temperature and ensure compliance with ANSI standards.
Disinfect Water Lines:
Disinfecting water lines periodically prevents bacterial growth, such as Legionella. Use approved chemical treatments and follow the manufacturer’s recommendations.
Lubricate Moving Parts:
Apply food-grade lubricants to valves and handles to prevent sticking or corrosion, ensuring quick activation during emergencies.
Common Issues and How to Address Them
Low Water Pressure:
Inspect the water supply line for kinks, blockages, or leaks. Ensure that the pressure meets the minimum requirements outlined by ANSI.
Corroded Components:
Replace rusted parts immediately to maintain structural integrity. Stainless steel components are more durable and corrosion-resistant in harsh environments.
Clogged Nozzles:
Mineral deposits or debris can block nozzles. To restore functionality, soak them in a vinegar solution or use descaling agents.
Frozen Pipes in Cold Climates:
Install insulated and heated enclosures to prevent freezing. Check heaters periodically to ensure they are operational.
Misaligned Spray Patterns:
Adjust nozzles to provide consistent coverage. The flow should reach both eyes simultaneously in an eye wash station and evenly cover the body in a safety shower.
How Often Should You Inspect Eye Wash Stations and Drench Showers?
Recommended Inspection Frequency
Weekly Activations:
Activate systems weekly to verify water flow, remove stagnant water, and detect immediate issues.
Monthly Inspections:
Conduct a thorough inspection of all components, including nozzles, valves, and water supply lines. Check for wear and tear, alignment, and overall functionality.
Annual Performance Testing:
Perform a comprehensive performance test annually to ensure compliance with ANSI Z358.1-2014. This includes measuring flow rates, assessing water temperature, and verifying equipment accessibility.
Documenting Maintenance for Compliance and Safety
Maintain Inspection Logs:
Document weekly activations, monthly inspections, and annual tests. Include dates, findings, and corrective actions taken.
Track Repairs and Replacements:
Keep detailed records of any repairs or component replacements. This helps identify recurring issues and assess the equipment’s long-term reliability.
Train Personnel:
Train employees on the proper use and maintenance of safety showers and eye wash stations. Ensure they understand the importance of accurate documentation.
Conduct Audits:
Regularly review maintenance records to identify gaps in compliance or recurring issues. Use this information to improve procedures.
Best Practices for Ensuring Safety and Compliance
Centralize Equipment Location:
Ensure safety showers and eye wash stations are easily accessible and without obstructions. They should be located within a 10-second reach of hazardous areas.
Install Alarms:
Equip systems with alarms to alert supervisors when a shower or eye wash station is activated. This ensures timely assistance during emergencies.
Use High-Quality Materials:
Opt for corrosion-resistant materials like stainless steel to prolong the lifespan of the equipment, especially in harsh environments.
Perform Emergency Drills:
Conduct regular drills to train employees to use safety showers and eye wash stations effectively. This reinforces muscle memory and preparedness.
Partner with a Trusted Supplier:
Choose a reliable supplier for durable and compliant safety shower systems. Collaborating with experts ensures you get high-quality products tailored to your facility’s needs.
Contact Us Today
Maintaining safety showers and eye wash stations is a crucial responsibility for any industrial facility. These systems save lives and minimize injuries during emergencies, making regular maintenance non-negotiable. By following these tips, you can ensure your equipment remains functional, compliant, and ready when it matters most.
At B-L-S Industries, Inc., we’ve been committed to workplace safety since 1976. Based in Carl Junction, MO, we understand the unique needs of industrial environments. From standard eye wash stations to custom-designed units and heated shower enclosures, we offer reliable, compliant, and durable solutions. Let us help you protect your employees and stay ahead of industry standards.